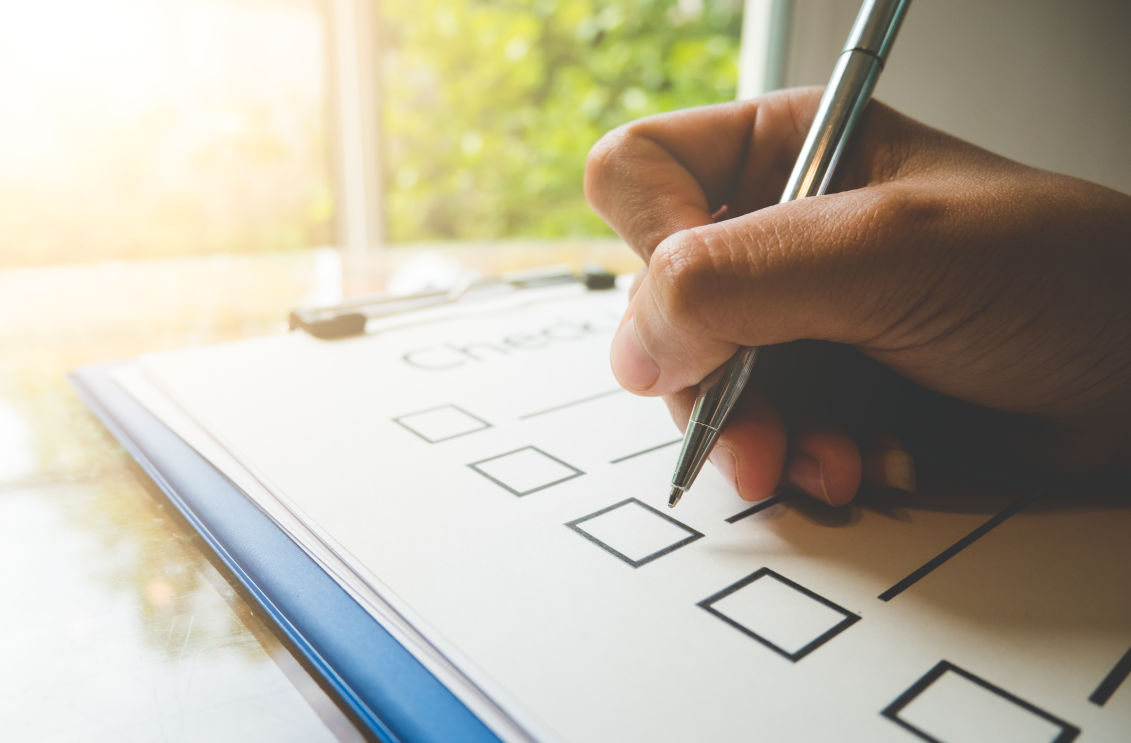
A thorough, effective workplace housekeeping plan sustained over time is a critical addition to any workplace. Unlike at-home housekeeping plans that prioritize aesthetics, workplace housekeeping plans prioritize safety and functionality.
This means employees are protected while doing their jobs. It also reduces businesses’ risk of lost productivity and earnings when employees cannot do their jobs well because of injury or improperly maintained machinery.
We created a housekeeping plan for the workplace to help you prioritize safety and function. Keep reading for tips to help maintain this plan long-term to protect your employees and business for years to come.
Why Is a Housekeeping Plan Necessary for Businesses?
A workplace housekeeping plan establishes a clear outline and checklist of best practices for maintaining safety standards. This ensures all employees are on the same page regarding what is needed and clarifies how and when each task should be completed. Maintaining a clearly written plan can also help you avoid tasks falling through the cracks and keep you from falling behind on regular maintenance requirements.
In addition to addressing how to handle acute issues that require immediate attention, a housekeeping plan creates an ongoing maintenance plan that helps you avoid reduced productivity when machinery breaks or injuries occur because of a missed safety hazard. With a robust plan, your business will be prepared for emergencies.
How Is a Housekeeping Plan for the Workplace Different From a Home Cleaning Plan?
While housekeeping at home usually addresses clutter and cleanliness, workplace housekeeping plans prioritize employee and customer safety and the functionality of machinery and processes. Although this includes some cleaning and decluttering, much like a housekeeping plan for the home, it is far more intensive and designed to save lives.
A workplace housekeeping plan often includes standards required by OSHA and other business regulating agencies. These help to ensure businesses remain compliant with industry regulations.
All of this adds up to financial gain for the business with savings on fines and fees as well as preventing lost revenue during shutdown periods because of injured employees or when good employees are unable to do their job because machinery is faulty or nonfunctioning.
7 Tips for Success & Safety in Your Workplace Housekeeping Plan
1. Stock, Maintain & Use Personal Protective Equipment
Employees are the greatest asset of every business and employee safety is essential. This starts with ensuring everyone on staff has personal protective equipment (PPE) appropriate to their tasks. It also involves ensuring PPE is stocked, in good working order and replaced as needed.
Not only should PPE be made available to employees while they are working, but management should also avail themselves of protective gear while implementing the housekeeping plan. This is important because they could come into contact with hazardous materials and dangerous areas.
2. Mitigate Slip, Trip & Fall Accidents
Slip, trip and fall accidents on the job can devastate everyone involved. Not only do employees endure the injury, but they are also unable to work for some time and may be inhibited in their ability to work long-term or gain promotions. Because accidents on the job mean that employees are unable to work, they can slow down productivity, halt projects and cut into the bottom line.
The housekeeping plan should include a full inspection of walkways, flooring and rugs at entrances and in any area where employees stand or work with hazardous materials. Any blockages to walkways should be moved, any broken or damaged flooring should be repaired or replaced and appropriate rugs should be in doorways and work areas.
3. Address Fire Hazards
Housekeeping plans must include a full review of fire safety plans and the tools needed to keep people in the building safe. This involves a review of equipment, exits and protocols.
Fire extinguishers should be available in all hazardous areas and graded for the chemicals or substances in use. Fire extinguishers should always be accessible, and they should be adequately maintained and replaced as needed.
Fire exits need to be available throughout the building and all walkways should remain free of debris and obstruction. Fire alarms and automatic sprinklers should be checked regularly per the housekeeping plan. Clear protocol for evacuating the building or handling a fire should be drawn up and reviewed with employees regularly.
Protocols should be in place to prevent fires in the business, especially when handling hazardous or combustible materials. Additionally, if the building is cluttered, it should be cleaned up and removed regularly.
4. Manage Dust & Waste
In some industries, dust is an air quality issue. Dust and unmanaged waste can be fire hazards. A layer of dust on surfaces can be a conductor for fire, and an overflow of waste can be the same.
Housekeeping plans should incorporate the installation and maintenance of industrial fans that can pull the dust out of the air and away from employees and surfaces. It should also include a waste management plan that ensures there are enough receptacles to provide a safe space to dispose of garbage and that there is sufficient hazardous waste disposal. The plan should ensure all waste is disposed of regularly and properly.
5. Stop Hazardous Material Transfer
Anywhere hazardous materials are used will require special cleaning agents and customized cleaning protocol. Mats used in those areas should be cleaned regularly and after every spill, no matter how minor.
If necessary, showering facilities, eyewash stations or other interventions for toxic material exposure may need to be installed and maintained as part of an overall housekeeping plan in the workplace.
6. Stop Falling Hazards
In warehouse settings with tall shelves, slick flooring, and large stacks of boxes, it is important to prevent items from falling onto employees. This starts with decluttering shelves and areas around shelves. It continues with ensuring all stacked boxes are secured with the proper railings and structures.
Heavy objects should be on lower shelves when possible and all objects should be pushed back from the edge of the shelf.
The layout and organization of storage and shelves should be set up for ease of access. During the implementation of the housekeeping plan, the layout and organization of items in storage should be assessed and double-checked.
7. Store Hazard Materials Safely
It is important to ensure employees are protected when using hazardous materials and can take care of themselves if their eyes or skin are exposed to toxic materials. It is also important to ensure all hazardous chemicals required for the business are stored safely. This reduces the likelihood of exposure.
Check the storage of all hazardous chemicals at the end of every shift. Housekeeping plans should follow up with that process and ensure employees are properly trained and regularly reminded of best practices regarding the use of toxic chemicals and other hazardous materials.
What Are the Best Practices for Maintaining a Housekeeping Plan in the Workplace?
Implementing a thorough, well-designed housekeeping plan is a great start, but it won’t help you manage any facility unless it is used properly. Here are a few additional tips to ensure your housekeeping plan is a success:
Add frequency to each item in the housekeeping plan. Some housekeeping tasks will require attention every shift, while others will need to be checked daily, weekly or monthly. It’s important to clearly indicate what needs to be done when and include a place to note the date of the last intervention. The steps taken should also be noted so the next person can access them to implement the housekeeping plan.
Write out detailed, step-by-step standards of practice. Commonly referred to as SOPs, these will help make sure everyone who completes a task on the housekeeping plan does so in the same way, using the same materials and with the same expectations and goals. These can be used to train employees and made available to anyone implementing the housekeeping plan.
Assign specific items on the housekeeping plan to specific people. Not everyone will be qualified to perform all the tasks required on the housekeeping plan, so make sure each task is assigned to a specific person to promote accountability and follow-through.
Maintain records. It is important to have a central location where everyone who implements the housekeeping plan can record the date and time they completed a task, what they found, how they responded and whether a follow-up is needed.
Create goals and expectations. There are certain things to look for in various aspects of the housekeeping plan. Machines will have an expected performance measure and require a certain amount and type of cleaning supplies on hand. Clearly define the expectations and goals. Make sure to include a place to note when they have been met.
Audit the housekeeping plan annually. Businesses change throughout the year. New machinery is incorporated, new processes and standards are developed and regulations change. The housekeeping plan should be updated annually to include all these changes, edit any SOPs that have not proven valuable and drop SOPs that are no longer necessary.
Make choices that support success for years to come. When choosing goals and processes for management of machinery and employee conditions and compliance, make choices that address big-picture goals and short-term concerns.
Don’t overlook the details. In light of the bigger maintenance and compliance issues, it is easy to forget the little things that must be addressed to facilitate the housekeeping plan. For example, make sure cleaning supplies are always topped off, rugs and mats meet the compliance standards of the industry and employees always have access to the PPE they need to do their jobs safely. The good news is that you can assign this task to Alsco Uniforms.
At Alsco Uniforms, we take care of the details so management can stay focused on big-picture projects. We can help you manage restroom supplies, uniforms, floor mats and cleaning supplies to make sure employees always have what is needed to get the job done.
To find out more about how we can help, call Alsco Uniforms today to discuss your needs. We are happy to help you manage your business needs so you can focus on what you do best — running your business.
References
Workplace Housekeeping: Basic Guide. Canadian Centre for Occupational Health and Safety.
Flammable Liquids. Occupational Safety and Health Administration.
General Requirements. Occupational Safety and Health Administration.
Housekeeping in the Workplace. National Ag Safety Database.